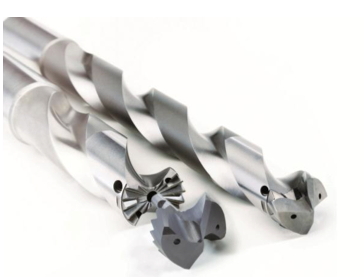
Replaceable head systems are indispensable today in modern production processes. Rising raw material prices, leaner stocks and the evaluation of the life-cycle costs rather than the pure purchase price are all factors in favour of replaceable head systems. MAPAL has placed highly productive systems on the market for all fields of application that are in no way inferior to monolithic tools – quite the contrary: With a focus on high-precision, very stable connection systems, MAPAL has succeeded in limiting the use of expensive carbide metal to the tool head, while still performing machining altogether stable and precise.
When it comes to drilling from the solid, MAPAL relies on the TTD replaceable head drill. At the focus – the torque transfer interface (TTS) that allows optimum torque transmission while at the same time achieving high changing and radial run-out accuracy. The TTD replaceable head drill thus achieves the performance level of a solid carbide drill, but at lower costs.
Success stories from a wide variety of fields of application and with different workpiece materials underline the performance of the TTD replaceable head drill. The 28 mm dia. fixing bores in gearbox housings of GJL-200, for example, are drilled with a TTD replaceable head drill from MAPAL. The customer's specifications with respect to the dimensional accuracy of the diameter can be optimally satisfied. The TTD achieves the real savings potential, however, with the doubling of the feed rate compared with the solid carbide drills used to date. 200 bores can be reliably drilled at 1,430 mm/min and with 140 m/min cutting speed with one replaceable drill head.
In one application from steel machining, supports for bending machines of St52 are drilled with the TTD replaceable head drill. 83 bores of 20 mm diameter and with a length of 106 mm have to be drilled in each part. Through the use of the MAPAL tool it was possible to reduce the machining time from 39.7 to 18.1 seconds – corresponding to a reduction in the machining time of 54%. Together with an increase in tool life of 77% and referred to the customer's annual production volume, the TTD reduces the costs per bore by 60%!
And there are successful examples of the use of the TTD replaceable head drill also in modern workpiece material combinations. For example, the machining of the bores for connecting a CFRP ship driveshaft to a steel hub. A combination tool from MAPAL with TTD solid drilling stage and a countersinking stage with PCD-tipped ISO indexable inserts enabled the machining time to be reduced by over 80%.
The change to the high-performance TTD replaceable head drill pays off in many areas – as confirmed by many success stories. Apart for a large bandwidth of workpiece materials, the TTD covers the drilling depths 1xD, 3xD and 5xD in the standard diameter range 12 – 45 mm, as well as the drilling depths 8xD and 12xD in the range 12 – 32 mm. Furthermore, the MAPAL specialists are at your disposal when it comes to special solutions.
|